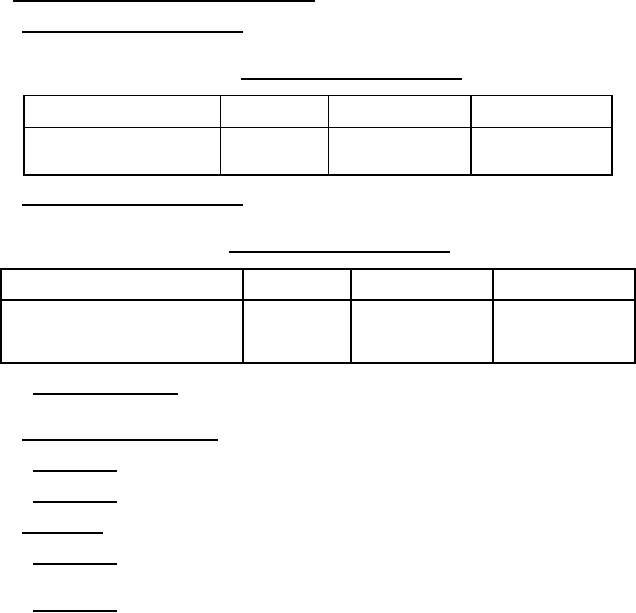
MIL-PRF-28861D
4.5 In-process inspection and conformance inspection.
4.5.1 In-process inspection (class B filters). Each production lot of capacitors manufactured for use in class B
TABLE IV. In-process inspection (class B filters).
Inspection
Requirement
Test method
Sample size
paragraph
paragraph
See MIL-PRF-31033
See MIL-PRF-31033
MIL-PRF-31033 In-process
Destructive physical analysis
See MIL-PRF-31033
See MIL-PRF-31033
4.5.2 In-process inspection (class S filters). Each production lot shall be inspected in accordance with table V.
Other screening inspections may be applied at the option of the manufacturer, as approved by the qualifying activity.
TABLE V. In-process inspection (class S filters).
Inspection
Requirement
Test method
Sample size
paragraph
paragraph
MIL-PRF-31033 In-process
See MIL-PRF-31033
See MIL-PRF-31033
MIL-PRF-31033 group A
See MIL-PRF-31033
See MIL-PRF-31033
MIL-PRF-31033 group B (except life)
See MIL-PRF-31033
See MIL-PRF-31033
Visual inspection
100%
4.5.2.1 Rework of class S filters. Rework of class S filters is not allowed unless the rework procedure has been
approved by the qualifying activity. Once a capacitor has been soldered in place, it shall not be reworked.
4.5.3 Inspection of product for delivery.
4.5.3.1 Class B filters. Inspection of product for delivery shall consist of group A inspection.
4.5.3.2 Class S filters. Inspection of product for delivery shall consist of group A and B inspections.
4.5.4 Inspection lot.
4.5.4.1 Class B filters. An inspection lot shall consist of all filters of a single PIN, produced under essentially the
same conditions, and offered for inspection at one time.
4.5.4.2 Class S filters. An inspection lot for class S filters shall be of one design. As a minimum requirement, the
lot shall consist of all the filters of a single part number representing one design and processed as a single lot through
all manufacturing steps on the same equipment, and identified with the same date and lot code designation. In
addition, the lot shall conform to the following:
a. Capacitors used in each filter of an inspection lot shall be traceable to one part number and one lot date
code (LDC).
b. Each element, such as toroids, ferrite beads, finished cases, end seals, and wire lugs used in the design of
the filter shall be from a single manufacturer and traceable to a single lot date code.
c. Solder for each application shall be of a uniform composition from a single supplier.
d. All single process operations shall be done during one continuous run without changes in temperature,
pressure, or other processing controls.
e. A lot identifying number shall be assigned at the time the lot is assembled. This identifying number (LDC)
shall be maintained through acceptance.
13
For Parts Inquires submit RFQ to Parts Hangar, Inc.
© Copyright 2015 Integrated Publishing, Inc.
A Service Disabled Veteran Owned Small Business